Weather Delays Are Draining Your Construction Budget
Your crew showed up ready to work—but now they’re stuck in their trucks, watching a downpour turn your construction site into a muddy mess. The concrete pour? Canceled. Equipment? Sitting idle. Your construction project timeline? Blown. Again.
Weather delays don’t just disrupt construction schedules—they throw off timelines, drain budgets, heighten safety risks, and cause costly downtime.
As a construction EHS manager, you know better than anyone how disruptive a single weather delay can be—with mounting costs that can rack up to thousands of dollars per day, with lightning alone accounting for more than $1 billion in annual economic losses.
Every EHS manager understands how any unplanned weather day can impact your project—whether it’s a near miss, a negative OSHA report, or a spike in your Lost Time Incident Rate (LTIR).
And when bad weather strikes, who pays? Your company? The contractor? The fine print in your construction contract?
But here’s the thing: weather may be out of your control, but its impact doesn’t have to be.
Perry Weather works with construction companies to proactively manage weather risks, incorporate weather days into their construction schedules, and keep crews safe—without costly delays.
In this guide, we’ll show you how to deal with weather delays on construction, account for weather days, optimize your schedule, prevent downtime, and save costs on your construction projects.
From Near Miss to Never Miss: Scheduling for Construction Weather Days
Every year, weather delays wipe out between 45 to 60 lost workdays of productivity on U.S. construction sites, leading to skyrocketing costs and expensive downtime.
For EHS managers, failing to account for inclement weather days can significantly impact a project’s safety record, leading to penalties, higher insurance premiums, budget overruns, and delays.
Why Near Misses Matter
A near miss in safety might seem like just a lucky break—an incident that could have led to injury or damage but didn’t.
But in reality, it’s a call for better systems, and when tracked properly with the right tools, near misses can be a leading indicator of workplace safety, helping EHS managers:
- Identify patterns in weather-related risks before they escalate.
- Optimize scheduling to reduce exposure to extreme conditions.
- Improve compliance & reduce liability risks under OSHA standards.
Unlike lagging indicators—which measure past incidents like OSHA recordables and LTIR—near miss data allows for proactive risk management and preventive action.
This proactive approach not only improves overall safety but also helps lower your lost time incident frequency rate (LTIFR), minimize weather-related downtime, and enhance compliance with OSHA standards.
Tracking LTIR: The Key to Preventing Weather-Related Incidents
OSHA mandates that employers must maintain extensive logs detailing incidents that led to injuries or lost workdays.
While weather might not be the first thing you think of when it comes to workplace injuries or lost time incidence rates, it should be.
- 🔥Extreme heat leads to dehydration, heat exhaustion, and dangerous falls.
- 🌧️ Heavy rain and wind create slip hazards, weaken structures, and stall critical tasks like concrete pouring.
- ⚡ Lightning is the deadliest weather threat for outdoor workers, forcing abrupt and costly work stoppages.
Construction projects across the United States face weather delays, and extreme conditions cause thousands of job site injuries every year.
That’s why tracking the Lost Time Incident Rate (LTIR) is critical—not just for compliance but for identifying preventable risks and improving safety protocols.
LTIR tells you how often employees miss work due to job-related injuries, incidents, or illnesses.
A low LTIR means a safer site, fewer disruptions, and a project that stays on track. A high LTIR can spell OSHA penalties, project delays, and reputational damage.
How to Calculate Lost Time Incident Rate (LTIR)
Calculating your organization’s Lost Time Incident Rate (LTIR) is simple—you only need two numbers:
- Total lost time injuries or lost time incidents in a given period
- Total hours worked in that period
Let’s break it down with an example:
Imagine your construction company records 800,000 total hours worked in a year, which is roughly equivalent to 400 full-time employees working for a full year.
Now, let’s say there were 10 lost time incidents during that period.
Here’s the formula:
- LTIR = (# of lost time injuries ÷ total hours worked) × 200,000
- LTIR = (10 ÷ 800,000) × 200,000 = 2.5
That means 2.5 lost time incidents per 100 full-time employees—a key metric for tracking workplace safety. The lower the LTIR, the better the safety record.
Want to calculate your LTIR instantly? Use our LTIR Calculator
What’s a Good LTIR for Construction?
- 📊 Industry Average: ~2.8
- 🏆 Best-in-Class Companies: Below 1.0
- 🚩 High-Risk Sites: Above 5.0
Although the construction industry’s average Lost Time Incident Rate (LTIR) is 2.8, best-in-class companies prove that significantly lower rates are possible, often below 1.0.
Weather-related incidents contribute significantly to the construction industry’s average LTIR, costing companies millions in lost productivity.
The Hidden Costs of a High LTIR
A high LTIR (above 5.0) often signals serious safety concerns, leading to regulatory issues, lost bids, and workplace culture issues.
It doesn’t just slow work; it drives up costs, risks lawsuits, and pushes workers out the door. Here’s why it matters:
- Project Delays – Every lost time incident creates bottlenecks.
- Rising Insurance Costs – Higher LTIR means higher workers’ compensation insurance premium rates.
- Legal & Compliance Risks – OSHA audits, lawsuits, and lost bids stack up fast.
- Workforce Retention – Unsafe job sites lead to high turnover and labor shortages.
Take this real-world example: In 2022, a large-scale construction project in Alabama faced heavy penalties and project overruns due to a high LTIR caused by heat-related injuries.
If weather risks had been accounted for, these incidents—and costs—could have been avoided.
How to Reduce LTIR and Improve Construction Scheduling with Perry Weather
To minimize LTIR, construction managers need to be proactive—not reactive—about safety and weather risk management with proper risk allocation and enhanced scheduling. Here’s how:
Plan for Weather Days
- Use Perry Weather’s historical and real-time weather data, along with the camera feed from the weather station, to anticipate potential weather delays. This way, remote stakeholders can also visually track and monitor current conditions.
- Build weather buffer days into construction project timelines to prevent rushed, unsafe work.

Use Real-Time Weather Alerts
- Don’t wait for storms, heat waves, or high winds to cause accidents.
- Get automated weather alerts and notify users with Perry Weather to instantly communicate critical directives to your crew before conditions become unsafe, preventing accidents and minimizing downtime.
Monitor Heat Stress in Real-Time
- Accurately Track Wet Bulb Globe Temperature (WBGT) with Perry Weather’s black bulb sensor and app.
- Adjust shifts, enforce hydration and cooling breaks, and proactively prevent heat-related lost time injuries and OSHA violations.
Optimize Work Shifts
- Schedule weather-sensitive tasks like concrete pours, roofing, and high-elevation work during low-risk hours.
- Use a flexible project schedule that adapts to changing weather.
Track Downtime with Data
- Use uptime/downtime tracking to analyze lost workdays and identify efficiency gaps.
- Use the LTIR calculator and log and analyze weather-related near misses to prevent future incidents.
So, how do you move beyond reactive measures and build truly weather-resilient construction schedules?
The answer lies in the precise, actionable weather data that Perry Weather delivers.
More Ways To Reduce Weather Delays & Lower LTIR with Perry Weather
At Perry Weather, we help construction EHS managers stay ahead of the weather and make smarter, safer decisions on the job site, minimizing lost time incidents, injuries, and costly downtime.
Whether it’s clearing the site before a storm or adjusting shifts for extreme heat, Perry Weather ensures your team stays safe—and your LTIR stays low.
Proactive Weather Day Planning
Instead of reacting to bad weather disruptions in your schedule, build it into your project plan from the start.
Precise Real-Time and Long-Range Forecasts
Perry Weather provides precise real-time weather data and long-range forecasts for your exact construction site instead of generic regional forecasts so you can identify potential weather threats days in advance and adjust schedules proactively.
Real-World Impact: “In the mornings, I get on the Perry Weather app and give the morning meeting, and I’m able to give these guys an accurate account of what they’re going to face that day… it all boils down to information.” – Donald Dennis, EH&S Manager for Leeward Renewable Energy
24×7 Met Support for Weather-Driven Planning
Perry Weather’s 24/7 meteorologist support gives you personalized insights on how incoming weather could impact major construction milestones or scheduled events.
Whether you’re planning a large-scale concrete pour, tower crane operation, or high-risk project, our team provides detailed guidance to help you adjust schedules, allocate resources efficiently, and reduce costly last-minute disruptions.
Plan Ahead with Historical Data
Analyze past weather trends for your specific location to determine the average number of weather days to build into your project timeline during the planning phase. This helps you create more realistic schedules and avoid costly overruns from the outset.
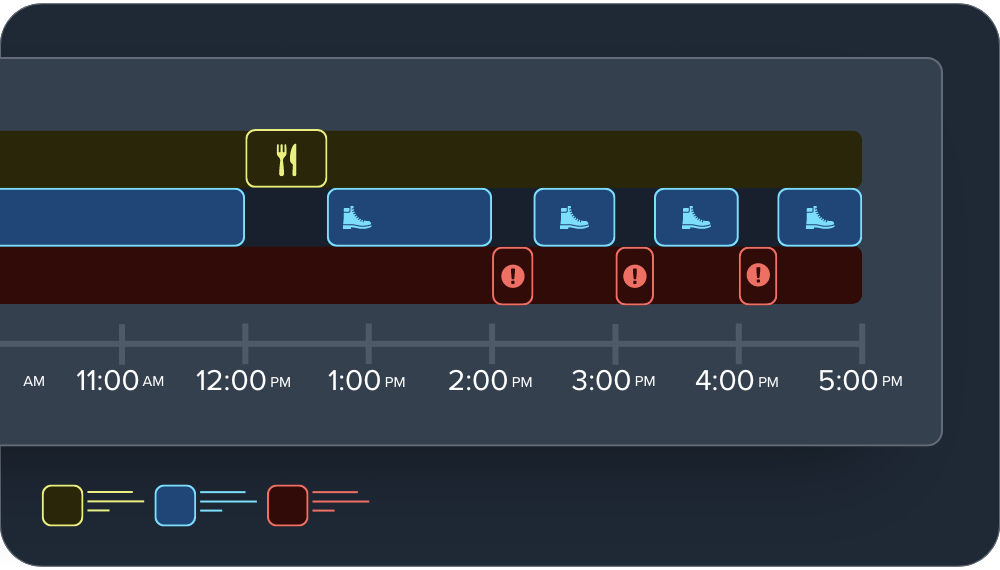
Wind Monitoring for Crane & High-Risk Operations
Sudden high winds can halt operations, create safety hazards, and result in major delays—especially for tasks involving cranes, scaffolding, or high-elevation work.
Perry Weather provides real-time wind monitoring and alerts to help you schedule lifts, rooftop installations, and other wind-sensitive tasks at the safest times.
Lightning-Fast Alerts
Backed by the National Lightning Detection Network (NLDN), Perry Weather’s customizable alerts notify you of lightning, so you can clear job sites before danger strikes, minimizing the risk of injury and lost time.
WBGT Heat Monitoring
With Perry Weather’s WBGT monitoring, you can proactively adjust work schedules and ensure hydration breaks during heat waves, preventing heat-related illnesses and keeping your LTIR low.
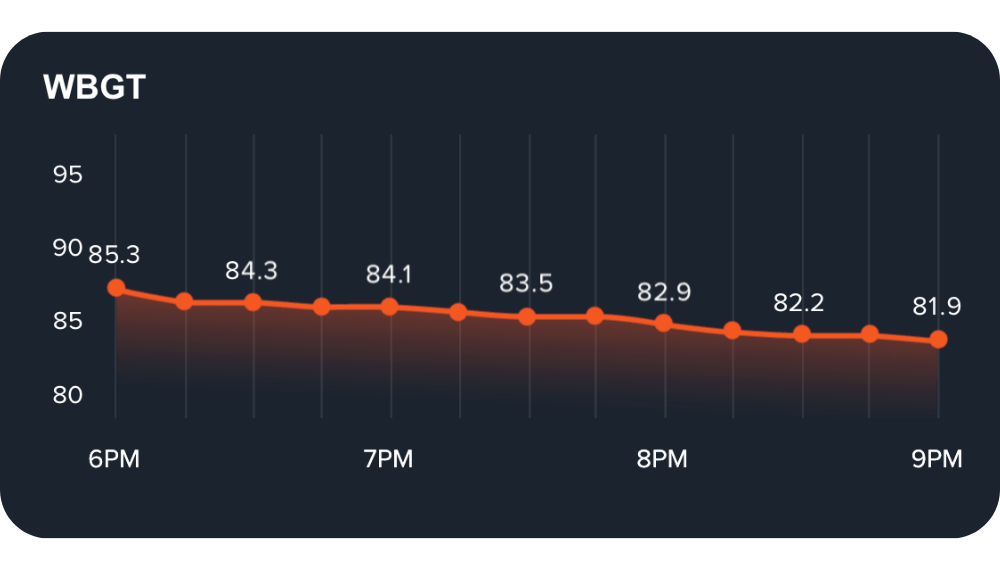
Real-World Impact
Texas-based Gridworks Construction struggled with heat-related downtime, costing thousands in delays.
They were able to significantly reduce downtime and saved thousands of dollars by adopting Perry Weather across their construction sites.
““Perry Weather is a big help to me because I don’t have to worry about the weather. Perry Weather alerts me on the heat, wind, lightning and storms coming.” – Shane Calloway, EHS Manager at Gridworks Construction
Incident Tracking & Compliance—Without the Hassle
No more manual tracking or compliance headaches—Perry Weather automates incident logging and simplifies OSHA reporting during near misses, helping EHS managers stay compliant, resolve disputes, and reduce LTIR—without the paperwork nightmare.

- Automatic Incident Logging: Heat stress conditions during near-misses and injuries are recorded instantly—no manual tracking needed.
- Simplified OSHA Compliance: Perry Weather automatically logs weather data for OSHA reporting, audits, and incident investigations.
- Dispute Protection: Perry Weather provides accurate, time-stamped data—along with camera feed snapshots from on-site hardware—to back your claims and resolve disputes quickly. Accurate records help defend against claims from contractors or insurers.
- Centralized Reporting: Quickly access and export incident logs in seconds for audits and internal reviews. Perry Weather easily integrates with your construction project management software for seamless tracking.
- Smart Scheduling: Plan weather-sensitive tasks—like concrete pours, roofing, or high-elevation work—at the safest times to cut downtime and keep projects on track.
Real-World Impact: “Perry Weather helps me stay focused on my daily duties, rather than being bogged down by paperwork, reports, and everything that EHS managers have to do to stay compliant.” – Shane Calloway, EHS Manager, Gridworks
With Perry Weather, you don’t just track incidents—you prevent them. Smarter compliance. Safer worksites. Less downtime.
Construction Weather Delays FAQs
What is a “near miss,” and why is it important to track in construction safety, particularly related to weather?
A near miss is an incident that could have resulted in injury or damage but did not. Tracking near misses, especially those related to weather conditions, provides a leading indicator of potential safety issues.
What are the main risks and costs associated with weather delays in construction projects?
Weather delays can disrupt timelines, increase budgets due to downtime and wasted labor, create safety hazards, and potentially increase a company’s Lost Time Incident Rate (LTIR). Specific costs can include idle equipment, canceled concrete pours, penalties from missed deadlines, and increased insurance premiums.
What are leading indicators?
Leading indicators are preventive measures that allow for proactive risk management. Near miss data is a leading indicator of workplace safety.
What are lagging indicators?
Metrics that measure past safety incidents, such as OSHA recordables or LTIR, used to evaluate past safety performance.
Take Control of Weather Risks Today
Weather is unpredictable—but your response to it shouldn’t be. Every lost workday or weather delay can cost upwards of $15,000+ per day in lost productivity, labor, and penalties.
If Perry Weather helps you prevent just 10 weather delays, that’s $150,000+ saved—ROI you can’t ignore.
With real-time alerts, heat stress monitoring, and automated incident tracking, you can:
- Turn near misses into never-misses with proactive safety measures.
- Manage weather risks before they overwhelm you.
- Protect your team, reduce costs, and ensure compliance—all in one platform.
Stop letting weather delays and downtime eat into your budget. See how Perry Weather can help keep your construction projects on track.
Sign up for a free trial or schedule a free demo today and take control of weather risks on your construction site.